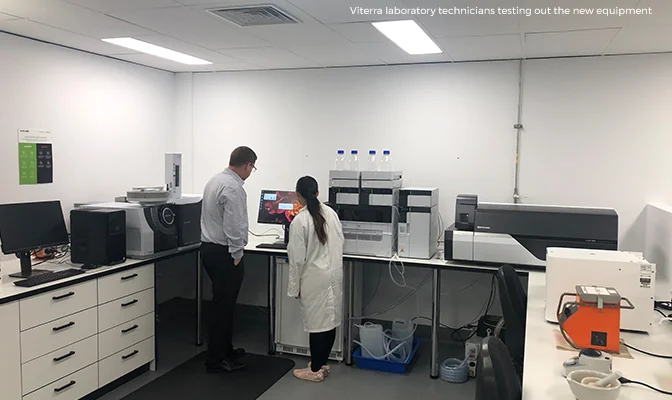
South Australian bulk storage and handling company, Viterra has been making major investments in quality over the last 18 months as part of its ongoing focus on food safety and quality management to meet customer needs.
End use customers are becoming increasingly discerned with quality, importing countries are tightening their regulations and maximum residue limits, and buyers are sourcing grain that is aligned with each of these needs.
Viterra has made a number of investments to help ensure the business continues to provide markets with consistent and reliable grain such as its purpose built laboratory, new chemical residue equipment, and maintaining strict and high standards of food safety and quality management.
Viterra Chief Operations Officer, James Murray, says the business has recently invested around $750,000 in chemical residue equipment.
“The new equipment means we no longer needs to outsource our chemical residue testing which previously could
“Bringing the testing in house allows us to be more efficient, which during the peak of harvest is important.”
“Harvest is a very busy time receiving the season’s grain, as well as undertaking a major accumulation task to outturn grain for domestic and export markets.
“Our new equipment means we can efficiently outturn grain and know which markets it is suitable for based on results from our chemical residue testing.
“Making sure we comply with importing country regulations and end use customer requirements is critical to ensure we continue to maintain market access for South Australian grain and its reputation.”
James says the new equipment follows other major investments made by the business including Viterra’s purpose built $3 million laboratory that was officially opened just over 12 months ago.
“Our laboratory is state of the art and undertakes testing to monitor all grain delivered into our storage and handling network,” James said.
“It has created efficiencies in monitoring and reporting back to sites which provides a more effective service to growers and end use customers.
“The laboratory has been built to manage an expanded range of services and testing to meet increasing customer demands well into the future.
“Our laboratory demonstrates to end use customers the extent of our quality and food safety focus in the Viterra supply chain.”
“The laboratory and all our other facilities in our network are ISO 22000:2018 accredited; the highest accreditation of any grain supply chain in Australia and meets the highest international standards in quality and food safety.
“Our ISO accreditation was audited late last year and approved to meet the new 2018 standards which includes greater accountability of process, monitoring and risk management for food safety and quality.
“Our accreditation and investments demonstrate our commitment to the South Australian grain industry and providing a valuable service to our grower and end use customers.”
Glencore Agriculture Senior Commercial Manager Lyndon Asser says he has hosted several delegates from international end use companies to tour the Viterra supply chain.
“Customers visit points along the supply chain from farm gate and upcountry receival sites through to Viterra’s laboratory and export terminals,” Lyndon said.
“When customers visit the facilities and see the processes through the network, it reinforces that they are sourcing quality, food safe grain from the Viterra network.
“End use customers are increasing their demand for quality, food safe grain and they want to know where it originated from.
“Taking customers to visit the facilities shows them that they are sourcing grain that goes through a rigorous testing process with stringent quality management processes.”